By Dhruv Krishna, Jal Jeevan Mission
In today’s water industry, the energy and enthusiasm are palpable, with industry veterans and domain experts providing solutions on an unprecedented scale. The key challenge is to maintain execution quality because water is a critical utility that demands round-the-clock attention.
India’s water industry is on an exponential growth path, with vast opportunities in untapped areas to manage this dwindling resource for its vast population. As 4G/5G networks continue to expand across the country, alongside improved accessibility through the development of road networks, the implementation of IoT and SCADA solutions becomes more feasible.
Government policies are aligning with the need to meet the water requirements of this immense population.
One significant development is the execution of large-scale turnkey projects, both greenfield and brownfield, across India’s water sector. The government is pursuing a two-pronged strategy: refurbishing old infrastructure and establishing new Water Treatment Plants (WTPs) and Sewage Treatment Plants (STPs) in areas previously lacking access to piped water, such as the Jal Jeevan Mission (JJM). A positive trend is the widespread adoption of technology, including IoT, Remote Monitoring Systems (RMS), and SCADA, to manage these extensive and remote utilities. The company has been a leader in SCADA and IoT solutions for the last 35 years. With extensive experience in water management, we’ve harnessed our knowledge to develop customized solutions and logic for remote asset management. Our hardware and software aim to enhance efficiency by preventing pumps from operating under abnormal conditions and averting water reservoir overflow. This is accomplished through smart logic and combinations of our level sensors and RTUs. We’ve also implemented vibration sensor-based anomaly detection and fault management for pump motors using machine learning and artificial intelligence. This provides clients with periodic updates on health and potential faults, ensuring preventive maintenance, reducing downtime, and improving efficiency. By preventing water wastage and enabling pumps to run at optimal levels through IoT and SCADA monitoring and control, we contribute to averting water scarcity and promoting sustainable water management.
The key technologies transforming the water industry and enhancing efficiency and sustainability are as follows:
- IoT and SCADA technology for remote monitoring and control of assets.
- Using AI and ML to improve pump efficiency, prevent breakdowns, and ensure continuous operation.
- Preventing pump motors from running in abnormal electrical conditions through protection relays and smart logic.
- Avoiding water wastage through overflow by using flowmeters, level sensors, and smart logic to shut down pumps based on water level and flow.
- Utilizing various instruments and methods, including membrane and check valves in STPs and WTPs to ensure healthy water for drinking and irrigation purposes.
Ensuring water quality is vital, and this is achieved through smart logic and sensors such as depth sensors, turbidity/chlorine sensors, and chlorine dosing pumps, providing clean and healthy water to end consumers.
To meet the water needs of India’s vast population, all potential sources of water, including groundwater and surface water, need to be tapped. Groundwater availability is decreasing as the population grows, necessitating the development of more surface water schemes. These schemes involve lifting and pumping water from natural sources like rivers, lakes, and ponds to large available land areas. The water is then treated at WTPs and used for drinking or irrigation. CIMCON Software India Pvt. Ltd has been a pioneering force in the implementation of SCADA and IoT technology for the automatic management of wastewater treatment plants with remote monitoring. Our extensive experience extends to multiple installations across India, where we efficiently manage nearly 540 million liters of treated water daily, catering to a population of approximately 12 million individuals.
Some of the notable cities where our services have made a substantial impact include Chandigarh, Ambala, Haryana, Pundri, Kullu, Manali, Palampur, Nagrota, Dharamshala, Sarkaghat, Chauntra, Thunag, Gandhinagar, Firozabad, and Lucknow, among others. These successful projects underscore our commitment to delivering smart wastewater solutions that address the critical water scarcity challenges facing India.
A typical Water Treatment Plant comprises the following parts and steps. To fully manage the plant, all stages need to be automated with Remote Terminal Units (RTU), sensors, and linked with SCADA software to enable seamless automatic operation with remote monitoring.
1. Raw Water
Details of Installations: Automation panel with RTU, ULT, 3 Phase actuators, and Flow meter.
- Raw Water from PST is collected in the Raw water sump.
- The system contains 3 pumps, 4 actuators, 3 pressure transmitters, and 2 level transmitters.
- Out of the three pumps, one is working while the others remain on standby.
- The measured Level in meters is compared with a predefined configured set value.
- During a predefined configured set time period for distribution, if the measured Level is within the limit set by the predefined configured value, the RTU will automatically command the automation panel to open the correlated actuated outlet valve and switch ‘On’ the correlated Motor pump.
- After the predefined configured set time period or if the measured Level falls below the limit, the RTU will command the automation panel to close the correlated actuated outlet valve and switch ‘Off’ the correlated Motor pump.
- All pumps and actuated valves can also be controlled from the web-based SCADA.
- Line Pressure and Energy consumption are continuously monitored in real-time using Pressure Transmitters and Energy Meters, respectively.
- The flow meter at the outlet of the pump house measures instantaneous flow in M3/Hour and cumulative flow in terms of M3.
Details of Parameters Monitored on Real-time Basis: Actuated valves status (Open/Close), Pump Status (On/Off), Pump Run Hours, Level (M), Line Pressure, and Electrical Energy parameters.
Outcome: Real-time monitoring and control lead to more efficient pumping processes and extended machinery lifespan due to optimized operation.
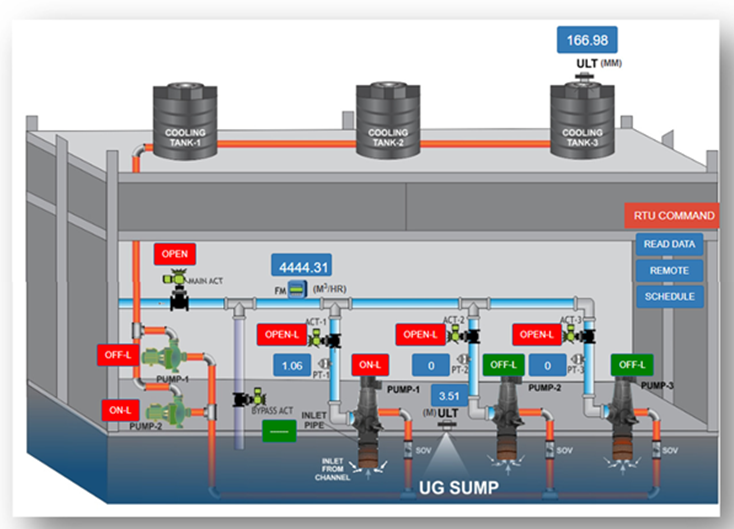
2. FLASH MIXTURE WTP
Details of Installations: Automation panel, flow meter, pH, turbidity, chlorine, and 3 Phase actuators.
- During a predefined configured set time period for distribution, the RTU will automatically command the automation panel to open the correlated actuated outlet valve and switch ‘On’ the correlated Flash Mixer.
- After the predefined configured set time period, the RTU will command the automation panel to close the correlated actuated outlet valve and switch ‘Off’ the correlated Flash Mixer.
- All Flash Mixers and actuated valves can also be controlled from the web-based SCADA.
- pH, Turbidity, and Chlorine are continuously measured in real-time using appropriate transmitters.
- The flow meter measures instantaneous flow in M3/Hour and cumulative flow in terms of M3.
Details of Parameters Monitored on Real-time Basis: Actuated inlet valve status (Open/Close), Flow (M3/Hour), Cumulative flow (MLD), Status & Run Hour of Flash Mixture, Flash Mixture (On/Off), pH, Turbidity (NTU), and Chlorine (ppm).

3. Clariflocculator
Details of Installations: Automation panel with RTU.
- During a predefined configured set time period for distribution, the RTU will command the automation panel to switch ‘On’ the flocculator.
- After the predefined configured set time period or if the measured Level falls below the limit, the RTU will command the panel to switch ‘Off’ the correlated flocculator.
- All flocculators can also be controlled from the web-based SCADA.
- Energy parameters are continuously measured and monitored using Energy Meters.
Details of Parameters Monitored on Real-time Basis: Run Hour of flocculator, flocculator (On/Off), Energy Parameter.

4. Filter Bed (total 12)/ Depends on the capacity of the plant
Details of Installations: Automation panel with RTU.
- After flocculation, water is fed to twelve filter beds.
- The level of respective filter beds is continuously monitored using ULT.
- The monitored Level is compared with a predefined configured set value.
- If the Level is within the limit, the RTU allows the actuated inlet valve and actuated supply valve to remain open, continuing normal filtration operation.
- If the measured Level exceeds the predefined configured set value, the RTU initiates the Backwash Process.
Backwash Process Sequence:
- Inlet valve and supply valve are kept open until head loss indication interrupts the process.
- Head loss is measured with the help of a level switch.
- Backwash is initiated, and inlet and supply valves are closed.
- Drain valve and air valve are opened, and the blower is started for a configured duration (e.g., 3-5 minutes).
- Air valves are closed automatically after the configured duration.
- Backwash valve is opened to feed clear water from the Backwash tank to the filter bed for a configured duration.
- The drain valve is closed, and inlet and supply valves are opened.
- Normal filter bed operation continues 24/7.
Blower System:
- Two blowers, one working and one on standby, are used for purging air to filter beds during backwash.
- Air pressure generated by blowers is monitored using pressure transmitters.
- Blowers are automatically turned on if a status signal is received from the RTU, and the air control valve is opened.
- Blowers operate sequentially.
- Blowers are automatically switched off if no status signal is received from the beds.
- Run hours of the blowers are maintained.

5. Backwash Pump
Details of Installations: Automation panel with RTU, Flow meter, Pressure transmitters, and Ultrasonic level transmitter.
- The system contains 3 pumps, 3 actuators, 1 Ultrasonic Level Transmitter, 1 flow meter, and 1 pressure transmitter.
- At a time, only 1 pump can run, selected by the RTU based on the last run pump.
- Ultrasonic Level Transmitter senses the tank level.
- Line Pressure and Energy consumption are continuously monitored in real-time using Pressure Transmitters and Energy Meters.
- The flow meter at the outlet of the pump house measures instantaneous flow in M3/Hour and cumulative flow in terms of M.

6. Clear Water Pump House
Details of Installations: Automation panel with RTU, ULT, 3 Phase actuators, Flow meter, pH meter, and chlorine meter.
- Clear Water from filter beds is collected in the Clear water sump.
- The system contains 3 pumps, 4 actuators, 3 pressure transmitters, 1 level transmitter, 1 Flow Meter, 1 pH meter, 3 Energy meters, and 1 chlorine meter.
- Out of the three pumps, one is working while the others remain on standby.
- The measured Level is compared with a predefined configured set value.
- During a predefined configured set time period for distribution, if the measured Level is within the limit, the RTU commands the automation panel to open the correlated actuated outlet valve and switch ‘On’ the correlated Motor pump.
- After the predefined configured set time period or if the measured Level is below the limit, the RTU commands the automation panel to close the correlated actuated outlet valve and switch ‘Off’ the correlated Motor pump.
- All pumps, the line Pressure, and Energy consumption are continuously monitored in real-time.
- The flow meter at the outlet of the pump house measures instantaneous flow in M3/Hour and cumulative flow in terms of M3.
- pH and chlorine are continuously measured in real-time using appropriate transmitters.

In Conclusion:
The implementation of digitalization and data-driven technologies like SCADA/IOT is crucial for efficient water treatment plant operation and management. These technologies provide real-time data on site conditions and parameters, water supply, quality, and equipment performance. This data is essential for justifying investments, ensuring sustainable water supply, and improving the health and lives of the people in India